Coventry’s battery sector set for major expansion
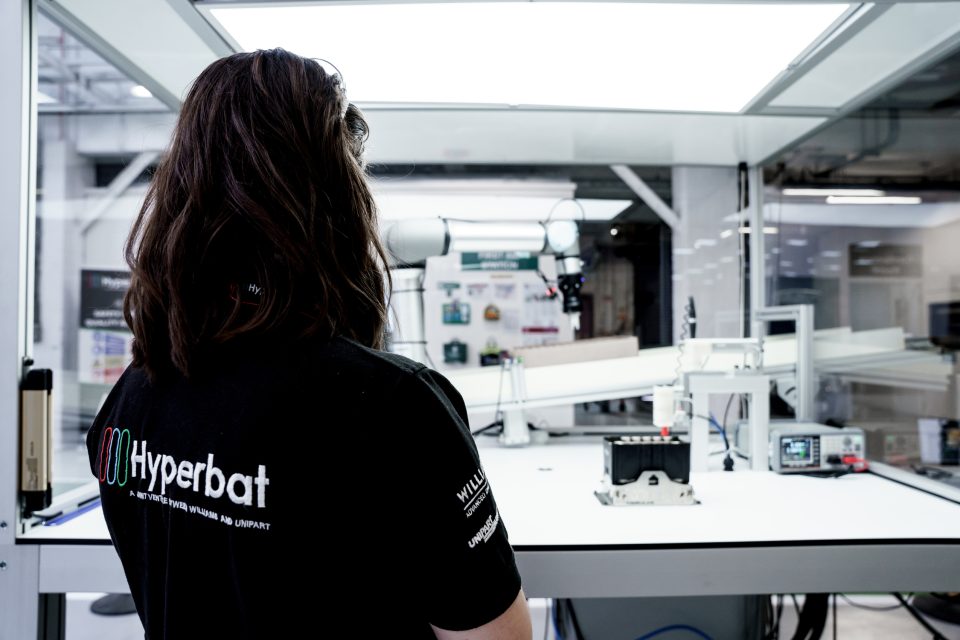
The H1perChain project, aimed at expanding the UK’s capabilities in battery pack manufacturing and supply chain, has been declared a resounding success.
This initiative, backed by the Advanced Propulsion Centre UK (APC) with an investment of £11.3 million, has achieved a significant milestone by developing an automated pilot line. This line includes module/pack assembly, cell joining, and in-line testing – crucial steps in reducing the costs and enhancing the scalability of high-performance batteries.
Hyperbat, leading the project in collaboration with principal consortium partners including Unipart Manufacturing, WAE, Coventry University, and Direc-Tec, has introduced a cutting-edge laser welding joining process for cylindrical cell formats. The project is not only technological but also educational, offering hundreds of skill development opportunities and establishing a digital platform to streamline the battery value chain.
With Hyperbat, a collaborative venture between Unipart and WAE Technologies, ramping up operations at Unipart Manufacturing’s Coventry site, it’s clear the company is gearing up to meet the soaring demand for high-performance, high-voltage battery solutions.
Jon Bell, project lead at Hyperbat, said, “We came into H1perchain with the overriding aim of developing a process and emerging supply chain capability for manufacturing high-performance batteries in the UK.
“The brief was to find a way of reducing costs while increasing performance and meeting lead times, something we believe we are well on the way to achieving with the pilot line successfully assembling packs and a ‘digital twin’ in play to scale up production into the tens of thousands.”
Over 50 specialised jobs have been generated at the Coventry production site, with plans to add another 25 roles following the first commercial contract to supply battery packs to an international client.
At Hyperbat in Coventry, the project’s concluding event saw attendance from over 50 representatives from various industry and academic sectors. Attendees were treated to a comprehensive tour of the pilot production line, showcasing advanced technologies such as incoming cell OCV testing, robotic stations for adhesive application, laser welding, potting machines, and robotic assembly. The event also included an immersive exploration of a digital twin, visualising a potential high-volume production facility.
Furthermore, H1perChain experts introduced their pioneering Industry 4.0 digitalisation platform, designed to bolster the UK’s capability to produce over £70m (approximately US$88m) in module and battery pack components and subsystems annually.
Bell added, “The Supplier Portal is one of the most exciting parts of H1perchain and gives us an IOT platform that the wider supply chain can now use to engage with Hyperbat on future activities. By creating a ‘single source of truth’ of key manufacturing process data, bills of material and quality accreditation requirements, we are making it easy for companies – looking to supply components into battery packs – to get involved.”
He outlined that the project has successfully integrated 36 UK suppliers into the system to date, with ambitions to expand this number to 200 by the end of 2024.
Sunil Maher, senior project lead at Advanced Propulsion Centre, added his support: “The H1perchain project has achieved significant and positive outcomes for the UK, with the consortium partners establishing battery module and pack manufacturing capability that is scalable for current and future demand.”